トヨタの EV 普及、カギ握る「出光の固体電解質」
出光のキーマンが明かす苦節 30 年の開発秘話
10 月 12 日、出光興産はトヨタ自動車と全固体電池の量産化に向けた数十人規模のタスクフォースを組み、量産化に向けた実証を進めると発表した。 2027 - 2028 年にトヨタが発売する EV にこの電池を搭載することも宣言した。 トヨタの佐藤恒治社長は「エネルギーの未来を変えていくために行動していきたいとの強い思いはまったく同じ」と述べ、出光の木藤俊一社長は「問われているのはポテンシャルや夢ではなく実現力。 出光は材料の製造、量産を通じて技術力で支えていく。」と応じた。
全固体電池の開発で先行するトヨタ
現在、電気自動車 (EV) やハイブリッド車のリチウムイオン電池では、イオンを移動させる媒体に可燃性の電解液が使われている。 これに対し、全固体の電池は固体電解質を電解液の代わりに使う。 エネルギー密度や安全性、耐久性が飛躍的に高まるとされ、EV 普及のカギになると言われる。
村田製作所や TDK などの電子部品メーカーはすでに全固体電池の量産体制に入っているが、これらは小容量の「酸化物系」で、容量は数十ミリアンペアの小型ボタン電池程度。 マクセルや日立造船は大容量が可能な「硫化物系」でそれぞれ 200 ミリアンペア時、5,000 ミリアンペア時(5 アンペア時)の全固体電池を開発するが、これも医療機器向けなどが中心だ。
これに対し、EV 向けの全固体電池は 30 - 40 アンペア時以上の容量が想定される。 世界の自動車メーカーは全固体電池の開発にしのぎを削るが、研究開発で先行しているのはトヨタだ。 トヨタは 6 月、10 分以下の急速充電時間で航続距離が現在の 2.4 倍になる全固体電池搭載の EV (約 1,200km 走行可能)を 2027 年にも投入する目標を明らかにしている。
全固体電池の核となる材料が、固体電解質だ。 製油所から石油精製の副産物として排出される硫化水素 (H2S) を原料にして、これに水酸化リチウム (LiOH) を反応させ、硫化リチウム (Li2S) ができる。 さらに五硫化二リン (P2S5) を反応させることで硫化物系固体電解質が製造できる (Li2S-P2S5-X)。 この「X」の組成が電解質の特徴のカギとなる。
出光は 30 年以上前から研究を進め、粒子の表面の形状などから柔らかいのに伝導度が高い(イオンの移動が速い)という特徴を持つ固体電解質の開発に成功した。 これがトヨタの求めていた密着性などが高く、体積変化に柔軟な固体電解質の特徴に合致した。 「耐久性に関する課題はとくに重要。 出光の固体電解質は粘り強く、柔らかい組成で精製されることが非常に大きなポイントだった。」と、トヨタの佐藤社長は会見で語った。
開発の発端は製油所から出てくる硫化水素
ただ、出光は一朝一夕にこの固体電解質にたどり着いたわけではない。 「開発の発端は、リファイナリー(製油所)から出てくる硫化水素にどうやってお金をつけて付加価値を上げるかということだった。 われわれとしては機能性樹脂の品ぞろえを広げたいという思いで開発をスタートさせた。」 こう話すのは、出光興産リチウム電池材料部の山本徳行主幹部員だ。 山本氏は出光興産の石油化学部門を経て 2008 年から一貫してリチウム電池の開発を主導してきた。
出光は 1970 年代のオイルショックを経て、世界中で石油資源の枯渇が叫ばれる中、代替エネルギーや素材開発を本格化する。 1981 年には研究所で「クンロク (96) 検討会」が発足し、15 年後の 1996 年を見据えた新規事業を模索する。 機能性樹脂の開発もその一環だった。 1990 年代に入り、研究所では塩素化されたベンゼンに硫化ナトリウム (Na2S) を反応させたポリフェニレンスルファイド (PPS) という機能性樹脂の開発を進めていた。 ただ、この方式では溶媒に溶けにくい塩が発生し、製造過程で扱いづらい。
このため、硫化ナトリウムの代わりに硫化リチウム (Li2S) を結合させる方式をある研究員が考案した。 このとき工業生産されていなかった純度の高い硫化リチウムを自らつくり出したことが、今日の固体電解質の開発につながる原点となった。 この研究で特許を出願したのが 1994 年。 出光が環境対応(低ベンゼン)ガソリン「出光ゼアス」を発売した頃だ。 しかし硫化リチウムの製造技術は確立したものの、電池への活用はまったく想定されておらず、PPS 製造での使用も途中で断念したため、硫化リチウムの用途は宙に浮く形となった。
大阪府立大学との出会いが転機に
7 年の雌伏の時を経て、大きな転機が 2001 年に訪れる。 当時、大阪府立大学で電解質の研究を行っていた辰巳砂昌弘教授(現大阪公立大学学長)が、この硫化リチウムにリンの添加物を加えると、伝導度の高い固体電解質ができることを発見したのだ。 「電池が全固体になるという発想がなかった時代だったが、(硫化リチウムが)固体電解質に結びついた瞬間、われわれのターゲットは電池になった」と山本氏は振り返る。
その後、大阪府立大と共同研究を重ね、2004 年には新しい組成を検討し、原料の純度を上げたことで電解液と同等のイオン伝導度を達成。 耐熱性にも優れていた。 2006 年には手作りの電池を試作して、国際電気自動車シンポジウム (EVS-22) の展示会に満を持して出展した。 「ところが、電池メーカー、自動車メーカーからは『この材料から大型で量産できる電池をいったいどうやってつくるのか』と言われ、さらなる実証を求められた。 材料の性能を示せれば、あとはメーカーが開発してくれるだろうと思っていたが、実証をしないと電池開発につながらないことを痛感した。(山本氏)」
電池メーカー「固体電池などやるわけがない」
それでも 2006 - 2009 年にかけ、電池メーカーに売り込みを図ったが、時は液系リチウム電池が盛り上がってきた時代。 「固体電池などやるわけがないだろうと言われ続けた(同)」という。 2009 - 2010 年には国際二次電池展でラミネート型(積層型)電池の見本をつくり、カーナビを動かすデモ展示も行った。 避難経路の看板や手術道具の熱殺菌などで耐熱性の高い電池にニーズはあったが、いかんせんニッチ。
だが、この頃から自動車業界で全固体電池への関心が高まっていく。 トヨタ自動車が電池研究部を立ち上げたのは 2008 年。 出光にとって全固体電池を実現するためのパートナーとして、開発、量産、販売を担ってくれることが必要だが、この 3 つの要素が 1 社で揃っているメーカーの一つがトヨタだった。 「(2013 年に)私がトヨタとの共同研究を決めた。 材料を広く売りたいという思いがあり、みんなと等距離でやるか、トヨタに集中するかはだいぶ悩んだ。」と山本氏は明かす。
「特許の状況などからみて、トヨタとの共同研究はありかなと判断した。 ただ、その後もほかのメーカーとも常にやりとりはしている。 今後もそのスタンスは変わらない。(山本氏)」 その後、10 年かけてトヨタと出光は「柔らかく伝導性の高い固体電解質」に磨きをかけ、ついに量産化へのメドをつけた。 出光は 2021 年に千葉県市原市の千葉事業所で、2022 年には同袖ケ浦市のリチウム電池材料部内に小型プラントを建設し、固体電解質のサンプルを製造してきた。 今回、千葉事業所で年産数百トンの大型プラントを新たに立ち上げ、量産化に向けた最後の実証を進める。
山本氏は「固体電解質は空気にも水にも触れさせてはいけない。 一昔前に比べて 1 桁小さな粒が要求される。 粉体は液系に比べてスケールアップが非常に難しい。 何が起きるかわからない。」と話す。
量産化のハードルは依然高い
それでも、両社は 2027 - 2028 年に全固体電池搭載の EV を実現することを宣言した。 量産化のハードルは依然高いが、残された時間は多くはない。 トヨタの佐藤社長は「今回の協業で材料の入り口から電池製品という出口まで一気通貫でやる。 ブレイクスルーを一体感を持ってスピーディーに実現していく。 最終的には日本の産業の国際競争力を高める。」と言う。 世界がしのぎを削る EV 向け全固体電池で、日本は市場を席巻することができるか。 両社の挑戦はいよいよ本番を迎えることになる。 (森創一郎、東洋経済 = 11-17-23)
EV 需要鈍化で巨額投資にブレーキ、テスラ含めメーカーに再考迫る
電気自動車 (EV) 需要に陰りが見えることで、業界トップのテスラも含め、急ピッチで拡大してきた EV 投資を見直す動きが広がっている。 メーカー各社は高級車志向の買い手のみならず、大衆車としての EV を目指し、北米であわせて約 1,000 億ドル(14 兆 9,400 億円)を投じる意向を示している。 しかし、インフレと金利上昇で、一般消費者が自動車を購入することは困難になっており、EV メーカーを取り巻く環境が悪化していることをうかがわせる。
例えば、フォード「F-150 ライトニング」は、連邦政府の税控除 7,500 ドルを加味する前の段階で約 5 万ドルからとなっている。 これに対し、同じ車種で基本モデルのガソリン車は約 3 万 7,000 ドルからだ。 ゼネラル・モーターズ (GM) の「シボレー・ブレイザー」は約 3 万 7,000 ドルからだが、EV なら税控除前で 5 万 6,000 ドルからとなっている。
こうした中、テスラのイーロン・マスク最高経営責任者 (CEO) は、メキシコに 10 億ドル規模の工場を新設する計画を先送りする可能性があると述べた。 昨年の成長ペースが 50% に上ったと胸を張って語っていた 3 月の投資家向けイベントからは様変わりだ。 GM はこれまで、デトロイト郊外の工場で電動ピックアップトラックの生産を拡大する計画を延期。 同工場では、来年から「シボレー・シルバラード」と「GMC シエラ」の電動ピックアップの生産を開始する予定だったが、現在では 2025 年後半まで開始時期が先送りされた。
フォード・モーターはすでに、EV 関連の投資計画 150 億ドルのうち、120 億ドルを延期すると発表済みだ。 ジョン・ローラー最高財務責任者 (GFO) は 10 月 27 日、ケンタッキー州で予定していた韓国 SK オンとの第 2 バッテリー工場共同建設を延期すると発表した。 フォードはまた、今年拡張したメキシコ工場での EV 車「マスタング・マッハ E」の生産を縮小している。 (David Welch、Bloomberg = 11-6-23)
ヤマト運輸、小型 EV トラック 900 台導入 大型の電動化には壁も
ヤマト運輸は 12 日、電気自動車 (EV) の小型トラックの新型車両を全国で今年度内に 900 台導入すると発表した。 脱炭素への意識が高まる中、物流の集配現場で普及が進んでいく見通しだ。 この日、群馬県高崎市の営業所で車両を公開した。 三菱ふそうトラック・バスが 3 月に発売した「eCanter」の新型モデルで、最大積載量は 2 トン。 1 度の充電で 116 キロ走れる。 ヤマト運輸の長尾裕社長は「住宅地や商業地が入り組んだ場所で、ラストワンマイルの主力になる」と話した。
2050 年に温室効果ガスの排出量実質ゼロを掲げるヤマト運輸は、EV の小型トラックについて、今年度内に累計 2,200 台とし、30 年までに集配を担う車両の約半数となる 2 万台まで増やす計画だ。 導入には、トラックなど商用車の電動化を促進する政府の補助金などを利用した。 事業を運営する環境優良車普及機構によると、9 社の 24 車種を対象に、今年度は 126 億円が計上されている。
一方、長距離の幹線輸送で主流の大型トラックは、EV の普及には時間がかかりそうだ。 大型車に対応する充電設備がほとんどなく、運行ダイヤが決まっていて分散利用できるバスとは違い、営業所内の限られた設備を使い回すのが難しい。 航続距離を長くために搭載する電池を増やさなければならず、燃費や積載効率に影響する。 そのため、現状では燃料電池自動車 (FCV) で、普及に向けた動きが先行している。 (高橋豪、asahi = 9-12-23)
テスラ・トヨタが採用表明「ギガキャスト」、リョービが試作の受託へ 50 億円で新工場
リョービは 11 日、国内最大級となる型締め力 6,000 トンクラスのダイカストマシンを導入すると発表した。 約 50 億円を投じて菊川工場内に新建屋を建設。 2025 年 3 月に稼働させる。 米テスラをはじめトヨタ自動車も採用を表明している巨大アルミダイカスト部品、いわゆる「ギガキャスト」向けで、自動車メーカーからの試作の受託を目指す。
新工場は敷地面積 3,400 平方メートル。 うち 1,600 平方メートルを鋳造工場とし大型ダイカストマシンを導入。 残り 1,800 平方メートルは金型工場とし、ダイカスト金型の加工や製作を手がける。 リョービはアルミダイカスト部品メーカーでは国内最大手級で、現在保有する最大の機械は同 3,500 トンだった。 電気自動車 (EV) では軽量化を目的にギガキャスト部品の採用が始まっており、こうした動きに対応する。 (NewSwitch = 7-13-23)
テスラの「カイゼン」 本家トヨタ学ぶ 新旧王者の逆転劇
電気自動車 (EV) 大手の米テスラが 1 日、創業 20 年を迎えた。 EV 最大手に上り詰める土台になったのは、2010 年に結んだトヨタ自動車との提携だ。 数年で解消したが、トヨタから初の工場と量産技術を手に入れた。 それから 13 年たち、今度はトヨタがテスラの生産技術を取り入れる。 2 社の関係は逆転した。 「ついに、トヨタもテスラから学ぶ。 ショックだった。」 6 月下旬、ある日本車メーカーの生産担当役員はこう漏らした。 「でも、このままでは EV の価格を十分に下げられない。 トヨタも造り方を変えなければならないところにきている。」
テスラの中核技術を意識
波紋を呼んだのは、トヨタが6月中旬発表した「ギガキャスト」と呼ぶ新技術だ。 大きな車体部品をアルミ鋳造で一体成型し、26 年の次期 EV で導入を検討する。 画期的だったが、テスラも同様の技術を「メガキャスティング」として採用している。 車体部品は従来 100 点超の板金部品を溶接などでつなぎあわせてつくってきた。
これに対し、テスラのメガキャスティングは大型ダイカストマシンで成型したわずか 2 点でつくれる。 20 年発売の「モデル Y」などで採用し、1 台あたり平均原価を半分にするのにつなげた。 中国の新興メーカーも追随したが、トヨタは距離を置いているとみられていた。 車を構成する部品の数が減れば、下請けの数も減るからだ。 「系列」で知られる自動車産業のピラミッド構造も崩しかねない。 だが、踏み込んだ。
テスラ躍進「誰も想像できなかった」
あるトヨタ幹部は率直にいう。 「テスラは EV の『マーケットリーダー』。 学ぶべきだ。」 だが同時にこうも付け加える。 「あのとき、テスラがここまでになるとは誰も想像できなかった。」 よぎるのは 13 年前のテスラとの資本・業務提携だ。 10 年 11 月、東京。 トヨタの豊田章男社長(現会長)との共同記者会見でテスラのイーロン・マスク最高経営責任者 (CEO) は満面の笑みで話した。 「世界トップのトヨタから学んでいる。」
この提携でトヨタから約 3% の出資を受け入れ、5,000 万ドル(約 70 億円)を調達した。 一方、生産終了したばかりのトヨタと米ゼネラル・モーターズ (GM) の旧合弁工場「NUMMI (カリフォルニア州)」の一部を 4,200 万ドルで買い取った。 当時、テスラは初めての完全自社開発車「モデル S」の量産に苦しんでいた。 生産のエキスパートがいない。業績も赤字続きで、手元資金も 1 億ドルあるかどうかだった。
そんなさなかに、ほぼ資金いらずの「居抜き」で工場が手に入ったのだ。 一部従業員も引き取った。 「フリーモント工場(旧 NUMMI)を手に入れる前は製造手法を知らなかった。 幸運だった。」 テスラ幹部はいまでもこう振り返る。 一方のトヨタ。 提携は章男氏のトップダウンで決まったとされるが、実りは多くなかった。 閉鎖工場の引き取り手は得たものの、協業の成果は共同開発 EV を少数売っただけ。 16 年末までにすべてのテスラ株を売却した。
トヨタの葛藤
トヨタはテスラの成長性に気付けていなかった可能性がある。 章男氏が提携を主導した理由は「動きが遅い開発部門に刺激を与えるためだった。(トヨタ幹部)」 だが開発現場は「EVはいつでもつくれる」という姿勢を崩さず、協業に乗り気でなかった。 17 年 6 月。 テスラと縁を切った直後の株主総会で章男氏はこう話した。 「テスラや中国勢が参入し競争相手とルールが変わろうとしている。 改革の指針は『微調整カイゼン』ではなく建設的破壊だ。」 建設的な破壊を次々と実現していったのは、マスク氏率いるテスラだった。
逆張りマスク氏、工場ごと「カイゼン」
テスラの成功の理由は、自動車産業の弱点と問題を突き止め、それと「逆張り」の戦略に徹した点にある。 新興企業で「レガシーコスト(負の遺産)」がない身軽さを生かした。 販売ディーラーを通さず、オンライン直販で車を売るのがその代表例だ。 ディーラーはきめ細かなサービスを消費者に提供する一方、車の価格を押し上げ、メーカーの負担にもなってきた。 競合の多くが販売網の見直しなどに苦慮するのを尻目に、テスラは 19 年に直販へ完全移行した。 「カイゼン」も発想を転換した。 生産現場で「1 円 1 銭」を切り詰めるのではなく、新工場を建てるたびに生産方式をゼロから見直す手法を採った。 「コスト 50% 削減」といった目標をつねに課し、社内外を追い込む。
「追う側」から「追われる側」に
下克上とばかりに EV 最大手にのし上がったテスラだが、明確な課題もみえている。 一つは大企業病リスクだ。 従業員は 12 万人を数え、年産能力は 200 万台に達する。 すでに大メーカーだ。 ベンチャーならではの型破りな経営は難しくなる。 陳腐化の懸念も忍び寄る。 23 年春には米国で主力「モデル 3」の中古価格が半年間で 20% も目減りした。 消費者もテスラ車に目新しさを感じなくなってきている。
反面教師にしてきた自動車業界は大きく変わりつつある。 中国メーカーが台頭し、異業種もなだれ込む。 追う立場から、追われる側へ。 最大手のトヨタすら踏み台にしてきたテスラだが、いまは逆にすべての車メーカーがテスラから学ぶ。 先頭を走る者の苦悩と重圧が向かい風となって吹きかかる。 (堀田隆文、nikkei = 7-1-23)
◇ ◇ ◇
トヨタとホンダが「EV 生産改革」でテスラを追撃 「ギガキャスト」や「モジュール構造」導入へ
「日本の自動車メーカーはまさにテスラ化している。」 ある大手自動車部品メーカーの幹部はそう驚きの声を上げた。 日本の自動車メーカーが EV (電気自動車)の競争で勝ち抜くために、生産工程の抜本的な見直しに取り組み始めた。 ガソリン車と異なる構造であることを重視し、車両の設計や構造、生産手法を根本から見直す。 見本とするのはEVで先行するアメリカのテスラだ。 トヨタ自動車は 6 月中旬に、次世代 EV に使用する車体部品について「ギガキャスト」の導入を検討していることを明らかにした。
ギガキャストは、車体部品を一体成形できる技術で、アルミダイキャストという鋳造法で溶かしたアルミ金属を流し込んだ金型を圧入して整形する。 アルミダイキャスト自体は既存技術だが、「ギガ = 巨大な」という言葉どおり巨大な装置で大型部品を作り出す。 別々に造った複数のパーツを溶接などでつなぎ合わせていたこれまでの工数、つまり製造コストを劇的に削減できる。
86 個、33 の工程が 1 つに集約
たとえば、トヨタが 2022 年に発売した EV「bZ4X」のリア部分は、86 個の鉄製の部品を 33 の工程で一体化している。 ギガキャストを導入することでアルミ合金製の 1 個の部品に置き換えて、工数は 1 に減らせるという。 トヨタの生産改革は、ギガキャストの採用にとどまらない。 次世代 EV では、現状のガソリン車や EV に比べて車体構造をスリム化・標準化する。 具体的には、車体をフロント、センター、リアの 3 分割した大きなモジュール構造とすることで、車種の開発や生産を簡単にできるようにする。
このうち、フロントボディとリアボディを前述のギガキャストで生産する。 さらにトヨタ生産方式の思想も盛り込むことで各工程の無駄を削減、効率化を徹底する。 トヨタで EV 事業を統括する BEV ファクトリーの加藤武郎プレジデントは、3 分割のモジュール構造とギガキャストの採用によって、「車両開発費と工場投資を削減できる」と自信を示す。 トヨタは、生産中の量産車が自走して次の工程を行う場所に移動する技術を開発中で、コンベアをなくして工場の設備レイアウトの自由度を拡張する。 デジタル技術や無人搬送機、自律走行検査の採用など、一連のクルマづくり改革で工場への投資金額、年単位でかかっていた量産準備の期間、工数を半減できるという。
EV の生産改革で先行するのがテスラだ。 テスラはイタリアのダイキャストメーカーである IDRA 社が供給する「ギガプレス」と呼ばれる巨大なアルミダイキャスト設備を使い、一般的な自動車メーカーなら 150 個を優に超える部品を、わずか 2 個に集約。 自動化も追求した高効率生産を実現している。 加えてテスラの場合、車種数の少なさ(現状 4 つ)や、原則ディーラーを通さない直販体制、広告宣伝に頼らない販売促進なども相まって、電池コストが高く利益を出すことが難しいといわれる EV で、好採算を実現している。
新たな生産手法をメキシコ工場に導入
さらにテスラは、「アンボックストプロセス」と名付けた新たな生産手法の導入を計画している。 シートやインストルメントパネル(前席正面の内装部品)、電装品も含め、車体を 6 つの大きなモジュールに分けて組み立て、塗装作業などもしたうえですべての部品を接合するというもの。 2024 年に稼働するメキシコ新工場で導入する。 投資額は 50 億ドル(約 7,000 億円)と巨額になるが、大幅な生産時間の短縮とコスト削減が可能になる見通し。 テスラが投入を予定する 3 万ドルを切る小型 EV はこのメキシコ工場で造る予定だ。
激化する EV 競争を勝ち抜くために、BYD や長安汽車といった中国勢もギガプレスの採用で走り出していた。 EV シフトとともに EV に最適化した生産改革でも出遅れていた日本勢で、巻き返しに動き出したのはトヨタだけではない。 関係者によると、ギガキャストの導入を検討しているのはホンダも同じだ。 ホンダは、2020 年代後半以降に投入する「MFD-BEV」と名付けた 10 車種以上で構成する次世代 EV 商品群の準備を進めている。 これらの商品群では、さらなる自動化やアルミダイキャスト部品の採用拡大といった新たな生産ラインが適用される見通しで、ギガキャストも導入が検討されている。
興味深いのは、ホンダも車体を 3 つのモジュールで形成するトヨタと似たような案を温めていること。 新ラインでは従来に比べて要員の 3 割削減、新車種に関わる費用を減らすなど飛躍的な生産効率の改善を図る。 また、温室効果ガスの排出量を減らすという。 三部敏宏社長は 6 月 21 日の株主総会の場で「2020 年代後半から次世代商品と合わせて、EV 専用ラインの生産システム改革に現在着手している」と語っている。 社内では、最終的には電池セルから完成車まで一貫して生産できる工場を 2020 年代後半に設置する計画が練られている。
EV で生産改革が進む切実な事情
自動車メーカーが抜本的な生産改革に取り組む背景には EV ならではの事情がある。 基幹部品である電池のコストがかさむため、ガソリン車に比べて採算が厳しい。 高価格帯が中心のプレミアムメーカーはまだコスト吸収余地があるが、大衆車メーカーはこれまでと次元が異なるコスト削減が必須だ。 ただ、そうした現実をわかっていながら、これまで日系メーカーは踏み出せなかった。 生産改革はメリットと同時にリスクもあるからだ。
たとえばギガキャスト。 一体成型された部品が破損した場合、まるごと交換することになるため修理費用が高くなるといった問題が指摘されている。 実際、テスラ車で高額な修理費用を請求される事例が報告されている。アフターサービスの充実や修理費用を含めたコストパフォーマンスを強みとしてきた日本勢だけに大きなハードルになると見られているが、トヨタ幹部は「衝撃をどう抑えるかも含めて対応策についてめどはついている」と自信を示す。
また、「ギガキャストが導入されれば、車体部品メーカーにとっては仕事がなくなる」と、ある車体部品メーカーの幹部は危機感を示す。 ギガキャストは部品点数と接合などの工数を減らし生産性を飛躍的に高める反面、当該部品や工程にかかわっていた部品メーカーにとっては仕事そのものがなくなる可能性がある。 トヨタやホンダはそれぞれ系列部品メーカーを抱え、密接な関係によるすりあわせの技術を生かし、緻密なものづくりを実現してきた。 が、ギガキャスト導入によって、強みとしてきたサプライチェーンにひびが入りかねない。 これはゼロからビジネスを構築してきたテスラとは異なる点だ。
莫大な投資も重荷になる。 ギガキャストや大型モジュール、さらなる無人化・省人化に対応した生産設備は、物の流れから人の導線まで既存の工場レイアウトの大幅な見直しも必要になる。 ホンダ幹部は、「世界中の工場で同じような設備を整えるには兆円単位の費用がかかる」と苦しい台所事情を吐露する。
反撃へ、トヨタは全固体電池を実用化
しかし、ここに来てリスクを恐れて足踏みしていられなくなった。 主戦場であるアメリカや中国は EV の販売台数が急激に増えており、先行するテスラは稼げる仕組みを整えつつある。 トヨタ幹部は「今までのやり方じゃ EV はとても儲からない。 テスラに徹底的に学んで(どうすれば儲かるか)わかってきた」と打ち明け、反撃に向け意欲的だ。 もっとも、テスラは CEO (最高経営責任者)であるイーロン・マスクのカリスマ性をブランド力の源泉として快走を続ける。 ソフトウェアサービスや自動運転でも既存の自動車メーカーにはマネのできないスピード感を持っている。
トヨタは、生産改革と同時に大幅に性能を高めた次世代電池を 2026 年以降に投入すると発表。 加えて、期待が高かった EV 向けの全固体電池も 2027 年以降に実用化する見通しを示した。 生産改革に次世代電池の量産立ち上げ、さらにはブランド力や商品力にどう磨きをかけるかも含めて、EV をめぐる競争が総力戦となることは間違いなさそうだ。 (横山隼也、東洋経済 = 6-23-23)
◇ ◇ ◇
テスラ採用の EV 車体一体成形技術、米谷製作所・共和工業が開発に挑む
米谷製作所(新潟県柏崎市、米谷強社長)と共和工業(同三条市、熊谷勇介社長)は、電気自動車 (EV) の車体を一体成形する「メガキャスト」を開発し、2024 年に同技術で使う超大型金型の提供を始める。 車体部品やバッテリーケースの成形を想定する。 米テスラなどが同様の技術を採用し、EV のコスト低減策として注目される。 日本製の高品質を強みとして、自動車メーカーへの金型提供を目指す。
メガキャストはアルミダイカストで EV の車体全体を一体成形する技術。 欧米や中国の EV 生産で部分的に実用化が進む。 テスラは約 70 点の部品で構成していた車体骨格部品をメガキャストにより 1 点に置き換え、コスト削減とともに車体剛性の向上につなげた。 米谷製作所と共和工業の取り組みでは、大型アルミニウム部品の成形時の型締め力で 4,000 トン相当、最大寸法 120 センチ x 100 センチ x 70 センチメートルに対応する。
これまで米谷製作所は自動車エンジン用などのアルミダイカスト金型を、共和工業は自動車のインスツルメントパネル用などの超大型樹脂射出成形金型などをそれぞれ開発・製造してきた。 メガキャストでは共和工業が部品の外形を作る主型を、米谷製作所が入れ子を製造する。 メガキャストの実用化には冷却時の歪みや空洞発生の課題がある。 そこで冷却時の収縮を予測した金型形状の設計や成形時の空洞発生を防ぐため金型内を高度な真空にするなど、加工条件の研究を両社共同で進める。
共同研究に先立ち、米谷製作所は超大型マシニングセンター (MC) など約 2 億円の設備投資を実施。 部品の内部形状を決める入れ子を最大 210 センチ x 170 センチメートルのサイズまで製造できる体制を整備した。 同社は 21 年 3 月にジョージフィッシャー中国と技術提携しており、メガキャスト分野の技術情報交換を進める予定だ。 今後、アルミ合金・マグネシウム合金などの成形材料や表面処理分野の国内企業も研究に参加する予定で、次世代 EV 向けの生産技術確立を目指す。 (NewSwitch = 4-15-23)
◇ ◇ ◇
EV の車体コスト、一体成型で 2 割減 UBE が製造装置開発
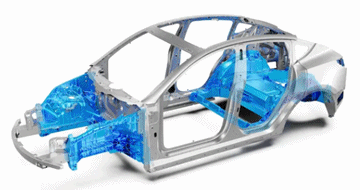
テスラは主力 EV 「モデル Y」の車体で、従来は約 170 個の部品(青い部分)だった
ところを、2 個のアルミ部品に置き換えた
UBE は電気自動車 (EV) の生産コストの削減につながる車体の製造装置を開発した。 車体に使う部品の 3 分の 1 ほどをアルミで一度に成型できる。 多数の部品を溶接する現在の手法よりも車体コストが約 2 割下がる。 欧州企業が開発で先行し米テスラが採用する一方、日本車は導入が遅れていた。 新製法の実用化で日本の EV のコスト競争力向上につなげる。
テスラ採用の一体成型、日本で実用化は初
アルミで車体の部品を一体成型する装置はイタリアの機械大手イドラが先行し、テスラが主力車に採用している。 テスラの生産性の高さを象徴する製造方式となっている。 日本企業で実用化するのは初めてになる。 国内の自動車大手が採用に向けた検討を始めた。
採用されれば数年後に発売される新型の EV に使われる見込みだ。 UBE の機械事業子会社の UBE マシナリー(山口県宇部市)が開発した。 アルミを溶かして大型の鋳型に高圧で流し込み、車体の骨格部分の 2 - 3 割ほどを一度に成型する。 これを鉄製の部品と組み合わせて車体をつくる。 これまでは数十個の鉄製の部品を溶接でつなぎ合わせていた。
高速で狙った量のアルミを射出、車体重量も 3 割軽く
溶けたアルミを高速で狙った量を射出する技術を強みとする。 新たに大きな金型でも正確に高速射出できるようにした。 鉄の部品がアルミに置き換わるため、車体の重量も 3 割ほど軽くできる。 価格は周辺機器を含めて 1 台あたり数十億円とみられる。 車体の骨格は EV のコストの 1 割超を占める。 テスラの場合、約 170個あった金属部品を 2 個の大型アルミ部品に置き換え、約 1,600 回必要だった溶接も不要になった。 溶接ロボットなども不要になるためコストが大幅に下がる。
米ゴールドマン・サックスによると、テスラの EV の原価は 2021 年に 3 万 6,000 ドル(約 480 万円)と一体成型を採用する前の 17 年と比べて半分になった。 EV は電池などの原価が高く、テスラなどを除いて利益を稼げていない。 電池や車体のコストをいかに下げるかが今後の競争力を左右する。 テスラに追随し、スウェーデンのボルボ・カーや中国の EV 新興企業なども一体成型の導入を計画する。 EV が欧米や中国で販売を伸ばすなか、低価格な EV の開発が焦点となっている。 テスラや中国の比亜迪 (BYD)、独フォルクスワーゲン (VW) などは低価格な EV の開発を進めている。 EV の商品化や品ぞろえで出遅れている日本車メーカーが価格競争力を高めるうえでも、EV 車体の低コスト製法の導入は課題となる。 (nikkei = 4-1-23)
パナソニックとマツダ、EV 向け車載電池供給で協力 年内に契約へ
パナソニックホールディングス (HD) とマツダは 21 日、電気自動車 (EV) 向けの電池の供給について、中長期的な協力体制をつくるために協議を始めたと発表した。 マツダが 2025 年以降に投入する新型 EV にパナソニック製の円筒形リチウムイオン電池を使うことを想定している。 HD 傘下で車載電池事業を手がけるパナソニックエナジーとマツダが 5 月末、意向書に署名した。 今年末までに正式な供給契約を結ぶことをめざす。
搭載する電池のサイズや数量などは未定という。 日本や北米の工場で生産する見通しだ。 パナソニック HD はネバダ州に EV 大手テスラと共同運営する工場を持っているが、カンザス州に建設中の新工場でつくる可能性もある。 マツダは 30 年に向けた経営方針で世界販売の EV 比率を 25 - 40% に高める計画を掲げている。 自前の電池工場は作らず、当面は他社と提携する方針を示していた。 パナソニック HD はマツダが 12 年からリース販売した「デミオ EV」に電池を供給していた。 パナソニック HD は車載電池事業を今後の成長の主軸ととらえ、30 年度までに生産能力を 22 年度比で約 4 倍に引き上げる計画だ。 (金子智彦、asahi = 6-21-23)
EV 「バッテリー」を取り巻く不都合な真実! 軽微な損傷で "全損扱い" 中古車悩ます過放電問題も
EV のバッテリー保証期間
電気自動車 (EV) のバッテリーには、一般的にバッテリーメーカー保証が付いている。 ドイツ自動車連盟のバッテリーメーカー保証を比較したデータによると、多くの自動車メーカーが「8 年、16 万km、容量 70%」を採用している。 それでは、メーカー保証期間を過ぎるとどうなるのだろうか。 例えば、日産自動車は 2018 年 3 月にバッテリーの有償交換プログラムを発表し、以下のような交換価格を公表している(価格改定により現在は金額が異なる)。
- 24kWh : 65 万円(再生バッテリー 30 万円)
- 30kWh : 80 万円
- 40kWh : 82 万円
メーカーのバッテリー保証期間を過ぎた場合の選択肢としては、
- 新車に乗り換える
- バッテリーを有償で交換する
- 保証期間が切れていることを前提で乗り続ける
のいずれかになる。 うがった見方をすると、EV は「8 年か 16 万km ごとに新車に乗り換える」ことを前提とすることで、商売として成り立っているともとれなくもない。 また、バッテリー保証期間を過ぎた中古車が、どのように取り扱われ、いくらで取引されるのかなどいまだわからないことも多い。 バッテリーの 8 年後、10 年後、さらには 15 年後の状態や、走行距離別の劣化度合い、あるいは中古車の扱いなど、EV の壮大な社会実験が、世界を巻き込んで現在進行形で行われている最中である。 メーカー保証期間を過ぎた EV の走行性能や安全性について、新たな知見待ちといったところだろう。
中古 EV を悩ます過放電問題
リチウムイオンバッテリーには、過放電の問題もある。 過放電とは、過充電とは逆に、バッテリーが長い期間充電されずに、放電しすぎることをいう。 リチウムイオンバッテリーには、使用していなくても自然と放電する自己放電という特性があり、過放電によりバッテリーのマイナス極に使用されている銅箔(どうはく)が溶け出す。 さらには、溶け出した銅と電解液が反応することで、バッテリーが膨らみ破損する可能性があるという。
ちなみに、手元にあるワイヤレスイヤホンの説明書でも、「長期間使用しない時は、バッテリーの劣化を防止するために、半年に 1 回程度の充電をするように」と注意喚起がされている。 EV のオーナーが適切なタイミングで充電を行っていれば問題がないが、長期休暇や中古車ディーラーによる長期間の放置により過放電となる可能性がある。 しかし、問題はその先にある。 EVのバッテリーが、過放電されたかどうか誰にもわからないということだ。
例えば、悪意のある元のオーナーが過放電したことを隠蔽したり、あるいは中古車ディーラーで売れ残って長期間充電されず放置されたりした場合、過放電によりバッテリーが劣化した中古の EV をつかまされるかもしれない。 もちろん、EV には充電記録が残る仕組みとなっている。 しかし、誰もが容易にアクセスできるものではないため、ドイツ自動車連盟はメーカーによる情報提供とバッテリー証明書などのルール整備が必要だと指摘している。
EV は保険料が高くなるという報道も
もうひとつ、EV のバッテリーの悩ましい問題は、事故にあったバッテリーの評価だ。 誰の目で見ても明らかに走行不能だと思えるくらい車体が損傷した場合はともかく、少しだけコツンと当たった、あるいは車体が少しへこんだ場合の、バッテリーの確認や安全性を担保する方法が置き去りとなっている。
2023 年 3 月 20 日付けのロイターの記事「Scratched EV battery? Your insurer may have to junk the whole car. (EV のバッテリーが傷ついた? 保険会社が車ごとジャンクにするかもしれない)」によると、バッテリーに軽微な損傷があっただけでも、修理や評価が難しく「全損扱い」となり、結果として EV の保険料が高くなるという。 バッテリーのリサイクルシステムが確立していない現時点では、評価ができずに廃棄された EV のバッテリーパックがたまる一方だ。
さらには、バッテリーの評価や再利用を断念してバッテリーパックの交換だけで済めば、ユーザーにとってまだ良いが、なかには、取り外しや交換が容易でない車両もある。 バッテリーの交換ができない車両は、ちょっとした事故でもバッテリーの評価や修理が不可能なためスクラップに直行することとなる。 バッテリーの交換が容易な EV づくり、EV 用バッテリーパックの規格化、バッテリーの診断など、解決は容易でないが克服しなければならない課題がまだまだ多い。
これから待ち受ける波乱の数々
ドイツの自動車メーカーのオペルは、独自に EV のバッテリー再生センターを設置し、専門的な教育を受けた技術者によるバッテリーの修理を行っている。 自動車メーカーが独自の規格でバッテリーを製造している現状では、第三者機関によるバッテリー修理は難しく、自動車メーカーの姿勢次第といったところだろうか。 また、EV バッテリーのリユースについては、日産自動車と住友商事との合弁会社である日本のフォーアールエナジー(神奈川県横浜市)がひとつの解答となるだろう。
EV のバッテリーパックは、バッテリーセル(電池に相当する小単位)を詰め込んだバッテリーモジュールを組み合わせて構成されている。 同社では、モジュール単位まで分解し、劣化度を測定した上で、劣化度が似通っているモジュールで再度バッテリーパックを作っている。 せめて、自動車メーカーの垣根を越えてバッテリーモジュールが共通規格となれば、リユースが進むのではないだろうか。
EV はまだ黎明期に過ぎず、歴史の 1 ページ目を刻んだところである。 この先、バッテリーだけでなく、ほかの EV の抱える課題によりひと波乱もふた波乱がありそうだが、EV の成熟に向けて健全な形での進化を望んでいる。 (小田坂真理雄、Merkmal = 5-17-23)
|